to engineering plastics
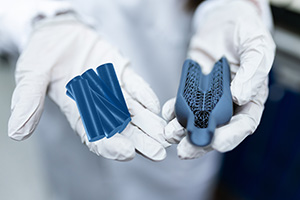

A VITAL ROLE
Examples of engineering plastics include polyether ether ketone (PEEK), polyphenylene sulphide (PPS) and polyamide-imide (PAI). These materials offer superior properties such as high strength, heat resistance, chemical resistance, and low friction.
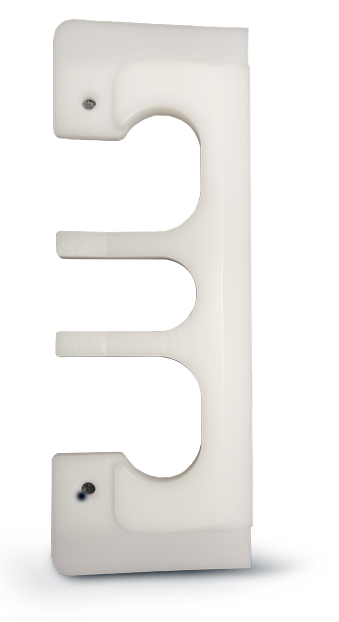
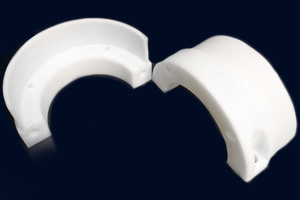
The right plastic for every project
In general, choosing the right engineering plastics for your project requires careful consideration of the specific needs of the project, the properties of each type of plastic, processing requirements and cost. Consult with our R&D on which engineering plastics would best suit your project.
likes to go through all steps

This is how we achieve the best result:
The first step is to determine the specific needs of your project, such as mechanical, chemical and thermal properties, and any other requirements, such as electrical conductivity or biocompatibility.
There are many types of engineering plastics, each with unique properties and characteristics. Some common types of engineering plastics include polyethylene, polypropylene, polyvinyl chloride, polystyrene and polycarbonate.
Once you have identified the types of plastics that may be suitable for your project, it is important to evaluate their properties, such as strength, stiffness, flexibility and chemical resistance, to determine which will best meet the requirements of your project.
The processing requirements of the plastic can also be an important consideration, as some plastics may require specific processing methods, such as injection moulding or extrusion, to achieve the desired properties and dimensions.
Finally, it is also important to consider the cost of the plastic, as well as all associated processing and production costs, to ensure the project stays within budget.